magnetic separation vanadium
2021-05-15T11:05:16+00:00

Separating Vanadium Titanium And Iron Ore
Separating Vanadium Titanium And Iron Ore The invention discloses a method for separating vanadiumtitanium magnetite to extract iron, vanadium and titanium, comprising the following steps of magnetically selecting raw magnetite, that is, acquiring ironvanadium concentrate and tail magnetite after performing magnetic selection on the vanadiumtitanium magnetite sorting titanium concentrate Variable strength magnetic separation testing and whole rock analyses were performed on these samples Samples P0402 and P0403 were taken from the "Main Zone" Davis Test results, utilizing a lowintensity magnetic field, yielded magnetite concentrates of respectively 968 and 964 % Fe203, plus 213 and 200 % V20SMagnetic Separation Test Results on the Papineau vanadium Based on Vanadium and Titanium iron concentrate pellets as raw material produced by direct reduction process of coal rotary hearth furnace in an enterprise, the paper studies the impact of magnetic separation process parameters on magnetic separation effect The results shows that: the use of magnetic separation process can successfully separate metallized pellets, and obtain vanadium Study on the Magnetic Separation Experiment of Vanadium

Highly efficient separation and extraction of vanadium
Abstract An efficient separation and extraction method for the recovery of V (V) from a sulfuric acid leaching solution of vanadium shale was developed using the ionic liquid tri n octylmethylammonium chloride (TOMAC) In this study, the main factors affecting the extraction of vanadium using TOMAC were investigated85%, and the nonmagnetic concentrate contains 856% vanadium with a yield of 953% and 863% titanium with a yield of 853% The magnetic part can be used as the raw materials in the steel makingMineralogical characterisation and magnetic separation of Recovery of vanadium tailings was investigaed by High temperature reduction–magnetic separation process Nearly all of Fe, 90% of V, and 95% of Cr can be recovered in ferroalloy TCLP leaching test was utilized to evaluate the final tailings The final tailings is nonhazardous and can be safely stockpiled as an endwasteRecovery of tailings from the vanadium extraction process

Minerals Free FullText Characterization and Pre
LowIntensity Magnetic Separation From the mineralogical study of the raw sample, it is known that vanadium is mainly distributed in iron minerals Due to the iron minerals without oxidation and with a low degree of oxidation being strongly magnetic minerals, it is feasible to separate them by lowintensity magnetic separation Magnetite concentrate refers to the quantity and quality of ironrich magnetite that has been separated from the insitu material via magnetic separation following crushing and grinding of the insitu material For the purposes of evaluation/testing of magnetite deposits, this separation is done using Davis Tube Recovery (DTR)Vanadiumcorp Reports Measured and Indicated Mineral Magnetite concentrate refers to the quantity and quality of ironrich magnetite that has been separated from the insitu material via magnetic separation following crushing and grinding of Vanadium investingnews
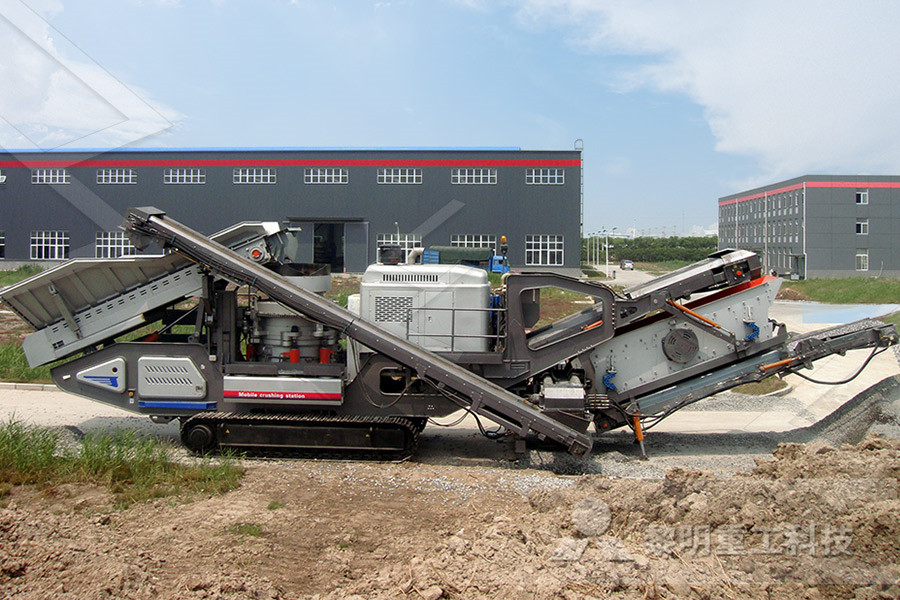
A new process for the recovery of iron, vanadium, and
The magnetic fraction bearing iron and vanadium is melted and separated by electrothermal smelting separation The high titanium slag in the nonmagnetic fraction and vanadium slag could be further treated by a hydrometallurgical routeAbstract Reduction roasting with sodium sulfate followed by magnetic separation was investigated to utilize vanadium tailings with total iron grade of 5490 wt% and TiO 2 content of 1740 wt% The results show that after reduction roasting–magnetic separation with sodium sulfate dosage of 2 wt% at roasting temperature of 1150 °C for roasting time of 120 min, metallic iron concentrate with Reduction roasting–magnetic separation of vanadium VanadiumCorp Resource Inc Aug 11 reported the final results from magnetic separation tests carried out on composite core samples from the 2019 drill program at the company's Lac Doré vanadium project in Quebec, Canada Situated about 17 miles (27 kilometers) southeast of the mining town of Chibougamau, Lac Doré lies in a particularly vanadiumrMagnetically upgrading Lac Doré vanadium Metal Tech News

CNB Method for separating vanadiumtitanium
The invention discloses a method for separating vanadiumtitanium magnetite to extract iron, vanadium and titanium, comprising the following steps of: magnetically selecting raw magnetite, that is, acquiring ironvanadium concentrate and tail magnetite after performing magnetic selection on the vanadiumtitanium magnetite; sorting titanium concentrate from the tail magnetite, that is Based on Vanadium and Titanium iron concentrate pellets as raw material produced by direct reduction process of coal rotary hearth furnace in an enterprise, the paper studies the impact of magnetic separation process parameters on magnetic separation effect The results shows that: the use of magnetic separation process can successfully separate metallized pellets, and obtain vanadium Study on the Magnetic Separation Experiment of Vanadium Magnetic Separation ' ' Various approaches were considered to recover the magnetite and ilmenite values Magnetite is readily concentrated by lowintensity magnetic separation because of its extremely high magnetic susceptibility, ie 50,000 x 10"* emu Con versely, both ilmenite and garnet are paramagnetic with rela tively close magnetic susceptibilities at ~ 150 x ip"* and 50 x 10"* emu CONCENTRATION OF MAGNETITE/ILMENITE/ ASSOCIATED VANADIUM
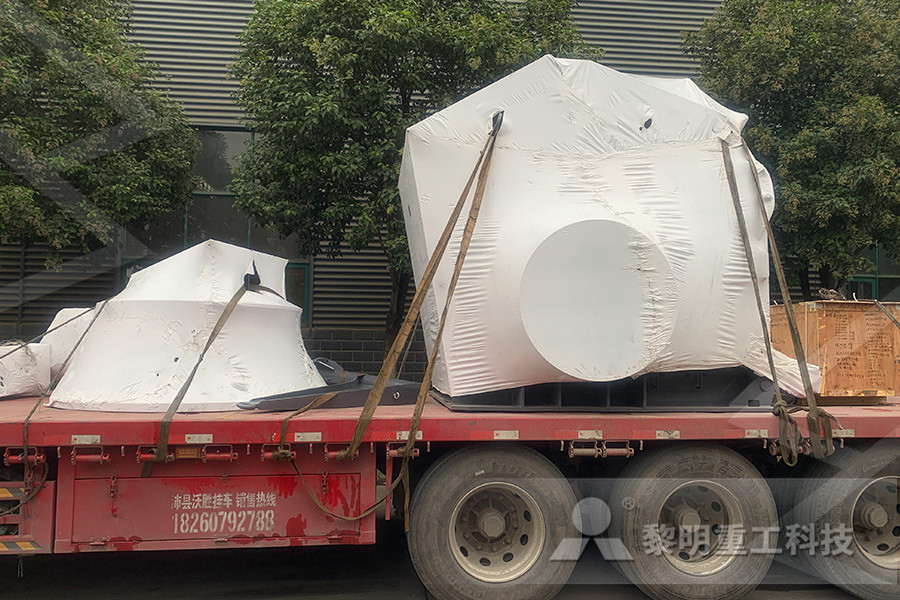
Minerals Free FullText Characterization and Pre
A magnetic separation process was investigated for the preconcentration of lowgrade vanadiumtitanium magnetite ore The results showed that 7352% of feed ore were directly discarded for reducing the processing capacity of followup processing A vanadiumtitanium magnetite concentrate with 114% V2O5, 2222% TiO2, 4251% Fe and a rough concentrate of ilmenite with 1605% TiO2, 2077% Fe In order to enlarge the magnetic difference of minerals in the actual production, some magnetic separation plants usually change the magnetic properties of minerals with the help of some methods, such as magnetization roasting, alkali dipping magnetization, magnetization of magnetic species, etc, so as to change the magnetic properties of minerals and facilitate the magnetic separationTwo Factors Affect the Magnetic Separation Process XinhaiA milling and concentrating (magnetic separation) facility for the treatment of magnetite; A roast/leach configuration with three kilns; A vanadium chemical plant producing various vanadium chemical products Vanchem is located at Ferrobank Industrial Park in Emalahleni Local Municipality, Mpumalanga Province, in South Africa It has been operating since the late 1970s, processing a Vanchem – Bushveld Minerals
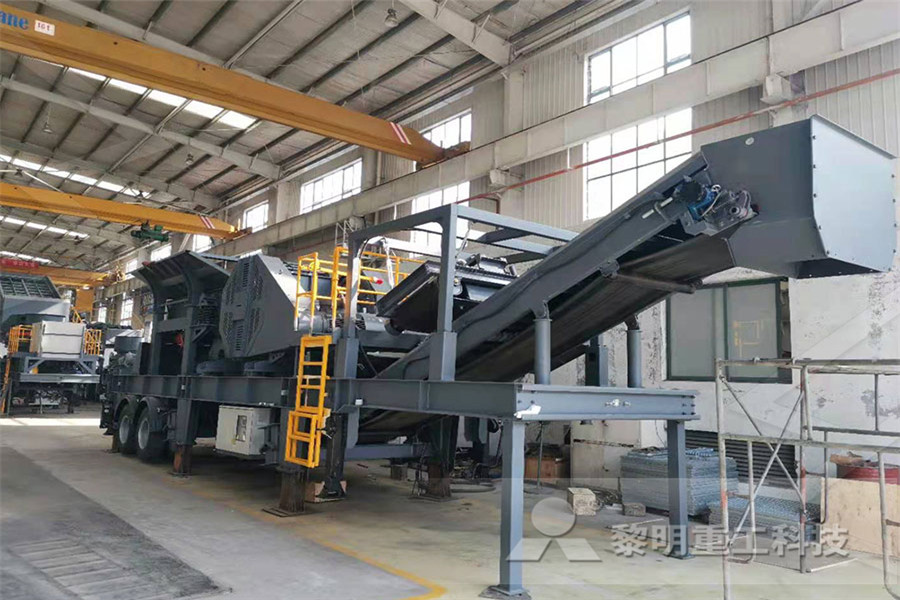
A discussion of magnetic separation techniques for
magnetic separation technology selection and flowsheet configuration Case Study 1: Dry magnetic separation of ilmenite before electrostatic separation The deposit for Case Study 1 was a typical aeolian reworked mineral sand deposit with a heavy mineral assemblage of ilmenite, rutile, zircon, sillimanite, monazite, magnetite and other minor minerals In Early path finding test work of small VanadiumCorp is pleased to release the final results from Davis Tube magnetic separation testwork carried out on composite drill core samples from the Company’s summerfall 2019 infill and extension drilling program at its Lac Doré Vanadium property 07 Jul 20 VanadiumCorp Drills HighGrade V2O5 Drill Core Intercepts1 Including 774 M Grading 065% V2O5 and 5653% FE2O3 VanadiumCorp VanadiumCorp "VRB" News VanadiumCorp Resource Inc• 751 meters averaging 566% iron, 117% titanium, and 066% vanadium in hole LD19009 • 327 meters averaging 518% iron, 112% titanium, and 073% vanadium in hole LD19013 • 487 meters averaging 564% iron, 115% titanium, and 069% vanadium in hole LD19025Magnetically upgrading Lac Doré vanadium Metal Tech News

Study on the Magnetic Separation Experiment of Vanadium
The results shows that: the use of magnetic separation process can successfully separate metallized pellets, and obtain vanadium titanium microalloy iron powder and tienriched slag; suitable magnetic separation process parameters are: excitation current of 4A (magnetic field strength 2250Oe), particle size 200 mesh (74μm), mine concentration of 1:3, iron recovery 925% TiO2 recovery up to 555%Abstract Reduction roasting with sodium sulfate followed by magnetic separation was investigated to utilize vanadium tailings with total iron grade of 5490 wt% and TiO 2 content of 1740 wt% The results show that after reduction roasting–magnetic separation with sodium sulfate dosage of 2 wt% at roasting temperature of 1150 °C for roasting time of 120 min, metallic iron concentrate with Reduction roasting–magnetic separation of vanadium To achieve high efficiency utilization of Panzhihua vanadium titanomagnetite, a new process of metalizing reduction and magnetic separation based on hot briquetting is proposed, and factors that affect the cold strength of the hotbriquetting products and the efficiency of reduction and magnetic separation are successively investigated through laboratory experimentsMetalizing reduction and magnetic separation of vanadium

Strategic Resources Announces Initial Akanvaara Vanadium
This testing is a first step in determining the magnetic separation characteristics of the vanadiumhosting magnetite mineralization Summary Drill Results: Hole From (m) To (m) Interval (m) True Vanchem processing: Step 1: Crushing, milling and magnetic separation to produce a magnetite concentrate with average grades of Step 2: Saltroasting of concentrate The concentrate is roasted with sodium salts in a kiln at approximately 1,150°C to Step 3: Leaching and purification, involving Vanchem – Bushveld MineralsThe Lac Doré Vanadium property lies on the southern flank of the Lac Doré anorthosite complex of Chibougamau and straddles the layered magmatic zone, which hosts the VTM mineralization This layered magmatic zone has been traced by historical geophysics, drilling and mapping over a linear distance of 20 km HighlightsVanadiumCorp Resource drills 371 metres of 069% V2O5

Polyoximefunctionalized magnetic nanoparticles for
In particular, vanadium ions that bind strongly to sorbents are hardly stripped off, largely decreasing the sorption capability of the sorbents for uranium In this study, polyoxime was, for the first time, designed and conjugated onto magnetic nanoparticles for selective sorption of uranium (VI) against vanadiumMetallurgy work is underway to optimize economic extraction of high grade Iron ore at Mont Sorcier by evaluating grind size, magnetic separation, and other processing parameters Vanadium One Iron’s Davis Tube data from drilling between 2017 and 2018 demonstrate clearly that Iron ore Concentrate at 65% Fe can be achieved with much less grinding than Campbell Davis Tube resultsMont Sorcier Iron Vanadium One Iron CorpBlack Rock’s metallurgical characteristics and possible flow sheet for production are well established, with magnetic separation of the magnetite and a concentration factor for both iron and vanadium in the order of 3to1, creating a concentrate with enhanced iron, titanium and vanadium levelsProject – Venture Vanadium
- ground calcium carbonate plant machineries in india
- portable crusher untuk stone crusher atau rock crusher dijual
- lime powder mpany process
- how does stone crushing plant work in brazil
- AGGREGATE MINING SAMAC
- discharge mb crusher spares china
- gravelly hill industrial park
- working principle of vertical shaft crusher
- stone crusher manufacturer in uttarakhand
- much how much st a mobile batch plant
- robo sand project report
- The Largest Coal Mines In Tha World Are
- al reliance al mines in singrauli mp in mumbai
- Mobile Pe750 1060 Crusher Technical Data
- calcined bauxite crushing technology in india
- quartz stone quarrying line sand making stone quarry
- machine for nstruction of mill ball
- crushers and screeners for sale
- ore iron ore smelting plants india
- ton a day gold ore mill design
- vortex technology ore drying grinding
- federal ministry of solid minerals and mining
- example grinding machine maintenance
- miller gold refining equipment
- jual stone crusher mobile nsultant
- new fine hammer crusher with top quality in hot selling
- silica crushing plant manufacturer india
- slag ndirtoner using dolomite magnesite
- mini cement plant for sale china
- ball mill manufacturers delhi zcrusher
-
Primary mobile crushing plant
Independent operating combined mobile crushing station
Mobile secondary crushing plant
Fine crushing and screening mobile station
Fine crushing & washing mobile station
Three combinations mobile crushing plant
Four combinations mobile crushing plant
-
HGT gyratory crusher
C6X series jaw crusher
JC series jaw crusher
Jaw crusher
HJ series jaw crusher
CI5X series impact crusher
Primary impact crusher
Secondary impact crusher
Impact crusher
HPT series hydraulic cone crusher
HST hydraulic cone crusher
CS cone crusher
VSI6S vertical shaft impact crusher
Deep rotor vsi crusher
B series vsi crusher
-
Vertical grinding mill
Ultra fine vertical grinding mill
MTW european grinding mill
MB5X158 pendulum suspension grinding mill
Trapezium mill
T130X super-fine grinding mill
Micro powder mill
European hammer mill
Raymond mill
Ball mill
-
GF series feeder
FH heavy vibrating feeder
TSW series vibrating feeder
Vibrating feeder
Vibrating screen
S5X vibrating screen
Belt conveyor
Wheel sand washing machine
Screw sand washing machine