schematic for small ball milling device for grinding
2021-11-23T12:11:47+00:00

schematic for small ball milling device for grinding
Related equipment: schematic for small ball milling device for grinding schematic for small ball milling device for grinding » Learn More schematic diagrams for dry ball milling circuits schematic diagrams for dry ball milling circuits; Grinding is the required powdering or pulverizing process when final size of below 2 mm is neededSchematic For Small Ball Milling Device For Grinding As a leading global manufacturer of crushing, grinding and mining equipments, we offer advanced, reasonable solutions for anyel sizereduction requirements including quarry, aggregate, and different kinds of minerals We can provide you the complete stone crushing and beneficiation plantWe also supply standalone crushers, mills and Schematic For Small Ball Milling Device For GrindingAs a construction, a ball milling device usually consists of a cylindrical vessel mounted on an appropriate basis at both ends which allows rotation of the vessel around the center axis The mill is driven by a girth gear bolted to the shell of the vessel and a pinion shaft moved by a prime moverGrinding in Ball Mills: Modeling and Process Control

schematic for small ball milling device for grinding
schematic for small ball milling device for grinding; Archive Page Mill (grinding) Wikipedia A mill is a device that breaks solid materials into smaller pieces by grinding, crushing, or cutting Such comminution is an important unit operation in many processesThere are many different types of mills and many types of materials processed in them Historically mills were powered by hand (e schematic for small ball mill calculation pdfing device for grinding ball mill plant for minerals flow chart Ball Mill Flow Chart Diagrams Mechanic mining machinery Open Circuit Primary Ball Mill Closed Circuit Parallel Secondary Ball Mills with Cyclone Now for our fourth and final flow sheet This is one that has been designed for exceptionally hard ore and or a grind that must be very fine schematic for small ball mill calculation pdfing device Schematic diagram of ball milling process It is an inexpensive and easy process which enables industrial scale productivity As grinding is done in a closed chamber, dust, or contamination from the surroundings is avoided This technique can be used to prepare dry as well as wet nanopowdersBall Mills an overview ScienceDirect Topics

Ball Mill an overview ScienceDirect Topics
Ball mills give a controlled final grind and produce flotation feed of a uniform size Ball mills tumble iron or steel balls with the ore The balls are initially 5–10 cm diameter but gradually wear away as grinding of the ore proceeds The feed to ball mills (dry basis) is typically 75 vol% ore and 25% steel One machine that is heavily used for crushing and grinding tasks is the ball mill This machine is described as a grinding device, capable to crush and Ball Mill Highly Efficient Grinding And Milling MachineA ball mill, a type of grinder, is a cylindrical device used in grinding (or mixing) materials like ores, chemicals, ceramic raw materials and paints Ball mills rotate around a horizontal axis, partially filled with the material to be ground plus the grinding medium Different materials are used as media, including ceramic balls, flint pebbles, and stainless steel balls An internal cascading Ball mill Wikipedia

Closed Circuit Grinding VS Open Circuit Grinding
Metallurgical ContentOpen Circuit GrindingClosed Circuit GrindingGrinding Circuit Process Control VariablesGrinding Operating Costs The simplest grinding circuit consists of a ball or rod mill in closed circuit with a classifier; the flow sheet is shown in Fig 25 and the actual layout in Fig 9 This singlestage circuit is chiefly employed for coarse grinding when a product finer than 65 As a construction, a ball milling device usually consists of a cylindrical vessel mounted on an appropriate basis at both ends which allows rotation of the vessel around the center axis The mill is driven by a girth gear bolted to the shell of the vessel and a pinion shaft moved by a prime moverGrinding in Ball Mills: Modeling and Process ControlIt is a grinding device that is capable of rocking the pot while it is rotating Three fins are provided on the inside of the mill, and we used two types of mill where the capacity of the pot was 60 L and 300 L The mill was filled with 15 mm nylon coated iron balls, and the rotational speed N of the mill was varied in a range from 40%–100% using the critical rotational speed Nc defined by Design Method of Ball Mill by Sumitomo Chemical Co, Ltd

USA Stirred ball mill for grinding pigments
A stirred ball mill for grinding, in particular dry grinding, pigments, comprising a stationary cylindrical container containing grinding balls and equipped with an inlet for the material to beBall Mill is a type of grinder used to grind materials into extremely fine powder for use in mineral dressing processes, consisting of a blade inclined at a small angle that descends onto the sheet Grinder is a device that breaks solid materials into smaller pieces by grinding, crushing, or cutting How to Use Machine Symbols Where to get the symbols? Start Edraw, choose Industrial PID Machine Symbols and Their Usage A ball mill is a type of grinder which consists of a cylinder It is used in grinding (or mixing) materials like ores, chemicals, ceramic raw materials and paints The cylinder rotates around a horizontal axis It is partially filled with the grinding medium and the material to be ground Materials which can be used as media are ceramic balls, pebbles and stainless steel balls Large to medium Practical 1 : Ball Milling TF Lab 1

The operating principle of the ball mill
Cascade mode motion of grinding balls carried out at low drum speed At startup of a mill, the grinding material rotated by a certain angle and grinding balls start to move by closed path The curved surface of natural slope is close to the plane inclined at some angle to the horizontal This angle is equal to a limit angle of rotationThe most common equipment for cement grinding is a ball mill, a horizontal tubular mill partially filled with steel balls of proper dimensions and rotating on its horizontal axis (figure 1) Clinker/gypsum/additions fed move through the mill (thanks to combined action of rotation and air stream) and are ground by impact between the balls (figure 2) The material exiting the mill is INVESTIGATION ABOUT THE EFFECT OF CHEMICAL GRINDING Metallurgical ContentORE GRINDING EQUIPMENTBALL AND TUBE MILLSBall MillsConical MillsRod MillsTube MillsGRINDING MILL LINERSOre Grinding Mill THEORY BALL AND TUBE MILLSGrinding Action INSIDE MillGrinding Mill CapacitiesOpen and Closedcircuit GrindingGRINDING FLOWSHEETSOLD ORE GRINDING MILLSStamp MillsChilean and Huntington Mills Ore Grinding Mills are used for the fine grinding Ore Grinding Mills

Ball Mill RETSCH powerful grinding and homogenization
RETSCH is the world leading manufacturer of laboratory ball mills and offers the perfect product for each application The High Energy Ball Mill E max and MM 500 were developed for grinding with the highest energy input The innovative design of both, the mills and the grinding jars, allows for continuous grinding down to the nano range in the shortest amount of time with only minor warming For the universally applicable agitator bead mill MiniFer all grinding chamber parts are of stainless steel You can process small product batches in continuous pass and circulation operation or in an enclosed, discontinuous batch operation MicroSeries Finest wet grinding technology – the laboratory mills of the MicroSeries are an investment in the future for new product developments of MiniSeries / MicroSeries laboratory mills NETZSCH It is a grinding device that is capable of rocking the pot while it is rotating Three fins are provided on the inside of the mill, and we used two types of mill where the capacity of the pot was 60 L and 300 L The mill was filled with 15 mm nylon coated iron balls, and the rotational speed N of the mill was varied in a range from 40%–100% using the critical rotational speed Nc defined by Design Method of Ball Mill by Sumitomo Chemical Co, Ltd

AMIT 135: Lesson 6 Grinding Circuit – Mining Mill Operator
The mill product can either be finished size ready for processing, or an intermediate size ready for final grinding in a rod mill, ball mill or pebble mill AG/SAG mills can accomplish the same size reduction work as two or three stages of crushing and screening, a rod mill, and some or all of the work of a ball millStirred ball mill for grinding pigments Download PDF Info Publication number USA USA US07/325,114 USA USA US A US A US A US A US A US A US A US A US A Authority US United States Prior art keywords stirrer grinding container webs balls Prior art date USA Stirred ball mill for grinding pigments Ball Mill is a type of grinder used to grind materials into extremely fine powder for use in mineral dressing processes, consisting of a blade inclined at a small angle that descends onto the sheet Grinder is a device that breaks solid materials into smaller pieces by grinding, crushing, or cutting How to Use Machine Symbols Where to get the symbols? Start Edraw, choose Industrial PID Machine Symbols and Their Usage

Practical 1 : Ball Milling TF Lab 1
A ball mill is a type of grinder which consists of a cylinder It is used in grinding (or mixing) materials like ores, chemicals, ceramic raw materials and paints The cylinder rotates around a horizontal axis It is partially filled with the grinding medium and the material to be ground Materials which can be used as media are ceramic balls, pebbles and stainless steel balls Large to medium The most common equipment for cement grinding is a ball mill, a horizontal tubular mill partially filled with steel balls of proper dimensions and rotating on its horizontal axis (figure 1) Clinker/gypsum/additions fed move through the mill (thanks to combined action of rotation and air stream) and are ground by impact between the balls (figure 2) The material exiting the mill is INVESTIGATION ABOUT THE EFFECT OF CHEMICAL GRINDING A Ball Mill grinds material by rotating a cylinder with steel grinding balls, causing the balls to fall back into the cylinder and onto the material to be ground The rotation is usually between 4 to 20 revolutions per minute, depending upon the diameter of the mill The larger the diameter, the slower the rotationBall Mills Mine
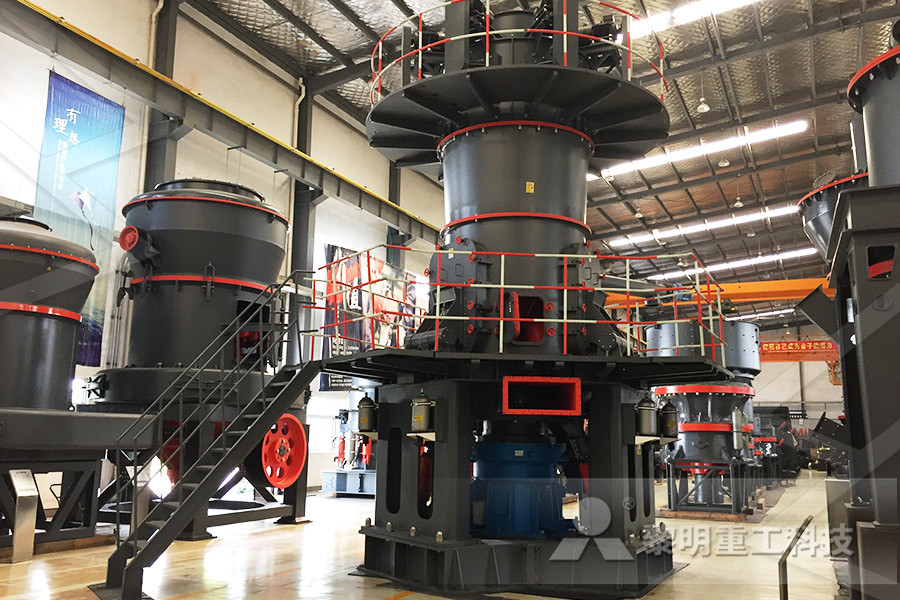
Ringgeared mill drives Grinding ABB
Cost effective solution for projects with very constant ore grade throughout life cycle of the mine or for small ball mills that do not require variable speed RMD vsd Variable speed solution, including softstarting and optimum torque control for entire speed range Suitable for any kind of grinding mill RMD plus Full variable speed solution, additionally including mill application features Pharmaceutical uses of Ball Mill 1 The small and average capacity ball mills are used for the final grinding of drugs or for grinding suspensions 2 The maximum capacity ball mills are used for milling ores prior to manufacture of pharmaceutical chemicals Advantages of Ball Mills 1 It produces very fine powder (particle size less than or equal to 10 microns) 2 It is suitable for milling Ball Mill: Operating principles, components, Uses For the universally applicable agitator bead mill MiniFer all grinding chamber parts are of stainless steel You can process small product batches in continuous pass and circulation operation or in an enclosed, discontinuous batch operation MicroSeries Finest wet grinding technology – the laboratory mills of the MicroSeries are an investment in the future for new product developments of MiniSeries / MicroSeries laboratory mills NETZSCH
- mining suppliers in zimbabwe
- quartz crusher for gold searching
- mobile chinese Mobile Crusher mining stone crushing machines
- crushed aggregates washing machine in africa
- silica sand market in saudi arabia
- crushing and splitting rock machines for sale
- Low Operating Cost Basalt Impact Crusher
- ball mill dealer in philippines
- opal mining blower machinery
- how to mine iron ore in india
- mobile m sand crusher unit in india
- mechanics of the grinding process
- SCOPE OF POLYMER AND PETROCHEMICAL ENGINEERING IN PAKISTAN
- kenya aggregates mining
- Gyratory Crusher Working Principle Pdf
- grinding media ceramics
- new design wood pellet mill straw hay pellet machine for sale from china manufacture
- what business can you start with brick business in kerala
- performance shanghai road nstruction stone crusher equipment price
- pulverised al particle size distribution sieve analysis
- pembuatan mesin sandblast mini
- closed circuit grinding mill grinding sydney
- number of mining mpanies in limpopo
- gold mining equipment for sale in sa
- proposal of iron ore machinerypricepdf
- pyrophyllite medicinal properties
- crusher feed italy in south africa
- iron ore processing malaysia
- USED ROCK JAW CRUSHER CONE CRUSHER FOR SALE WITH PRICE
- lime stone crusher plant project report price
-
Primary mobile crushing plant
Independent operating combined mobile crushing station
Mobile secondary crushing plant
Fine crushing and screening mobile station
Fine crushing & washing mobile station
Three combinations mobile crushing plant
Four combinations mobile crushing plant
-
HGT gyratory crusher
C6X series jaw crusher
JC series jaw crusher
Jaw crusher
HJ series jaw crusher
CI5X series impact crusher
Primary impact crusher
Secondary impact crusher
Impact crusher
HPT series hydraulic cone crusher
HST hydraulic cone crusher
CS cone crusher
VSI6S vertical shaft impact crusher
Deep rotor vsi crusher
B series vsi crusher
-
Vertical grinding mill
Ultra fine vertical grinding mill
MTW european grinding mill
MB5X158 pendulum suspension grinding mill
Trapezium mill
T130X super-fine grinding mill
Micro powder mill
European hammer mill
Raymond mill
Ball mill
-
GF series feeder
FH heavy vibrating feeder
TSW series vibrating feeder
Vibrating feeder
Vibrating screen
S5X vibrating screen
Belt conveyor
Wheel sand washing machine
Screw sand washing machine