cement industry production kiln
2023-03-06T13:03:22+00:00

The cement kiln
Manufacturing the cement kiln Wet process kilns The original rotary cement kilns were called 'wet process' kilns In their basic form they were Dry process kilns In a modern works, the blended raw material enters the kiln via the preheater tower Here, hot gases The clinker cooler There Cement kiln dust (CKD) is an industrial waste material collected from cement kiln exhaust gases during Portland cement production In the production of Portland cement, clay and calcium carbonate are finely ground, mixed and calcined at 1450 °C During this process, calcium silicate is the main product formed and a dust named CKD is generatedCement Kiln an overview ScienceDirect TopicsIn environmental protection, the use of cement kilns is to incinerate hazardous wastes and wastes and realize waste discharge been unharmful, and waste is used as fuel to save coal powder Cement Production Line, Cement machinery, Rotary kiln

Cement Kilns: A Ready Made Waste to Energy Solution
Due to the nature of cement production, cement kilns require temperatures of 2000°C in their main burner Excellent conditions for waste derived fuels, they have become a standard fuel for many cement kilns around the world But there is potential for this to grow fivefoldAGICO is specialized in design and supplies equipments for complete cement production lines of different scales, capacity from 300 to above 2500TPD; Main equipments include: rotary kiln, grinding equipment (ball mill and vertical mill), crusher(Jaw Crusher, Impact Crusher, Hammer Crusher), cooler (Rotary Cooler), preheater (Cyclone Preheater), dust collector, conveyor equipments, etcLeading Supplier of Cement Plant Equipments Rotary Kiln Waste Incineration in Cement Kilns The cement industry is actively seeking to increase the use of alternative fuels for cement production Both to decrease energy dependence on conventional fossil fuels and to mitigate negative environmental impact One of these alternatives is wastetoenergyCement Production : Gasmet

Cement Manufacturing Process Phases Flow Chart
Kiln is a huge rotating furnace also called as the heart of cement making process Here, raw material is heated up to 1450 ⁰C This temperature begins a chemical reaction so called decarbonation In this reaction material (like limestone) releases the carbon dioxideThe cement industry is the third largest user of coal after the steel and power industries and it consumes more than 5% of total coal produced in India This coal requirement will go up further with the rapid expansion of the cement industry (for infrastructure projects) Coal is the principal source of fuel for cement kilnsCement Industry an overview ScienceDirect TopicsCement production and concrete as building material The properties of concrete make it a primary building material where reliability and durability are required Depending on the application ~ 300 kg cement are used for 1 m3 of concrete The cement industry emits ~ 7% of global anthropogenic CO 2 emissions China >50% Cement plant with rotary kiln, preheater tower and raw material grinding Process characteristics of clinker and cement production

Analysis of the process of cement rotary kiln LCDRI CN
The cement production process uses a new dry cement preparation process, which is mainly composed of crushing and prehomogenization, raw material preparation and homogenization, preheat decomposition, cement clinker firing, cement grinding and packaging, etc And grind, or dry and grind into raw meal powder, then feed the raw meal powder into the cement rotary kiln to calcinate the Due to the nature of cement production, cement kilns require temperatures of 2000°C in their main burner Excellent conditions for waste derived fuels, they have become a standard fuel for many cement kilns around the world But there is potential for this to grow fivefoldCement Kilns: A Ready Made Waste to Energy Solution AGICO is specialized in design and supplies equipments for complete cement production lines of different scales, capacity from 300 to above 2500TPD; Main equipments include: rotary kiln, grinding equipment (ball mill and vertical mill), crusher(Jaw Crusher, Impact Crusher, Hammer Crusher), cooler (Rotary Cooler), preheater (Cyclone Preheater), dust collector, conveyor equipments, etcLeading Supplier of Cement Plant Equipments Rotary Kiln
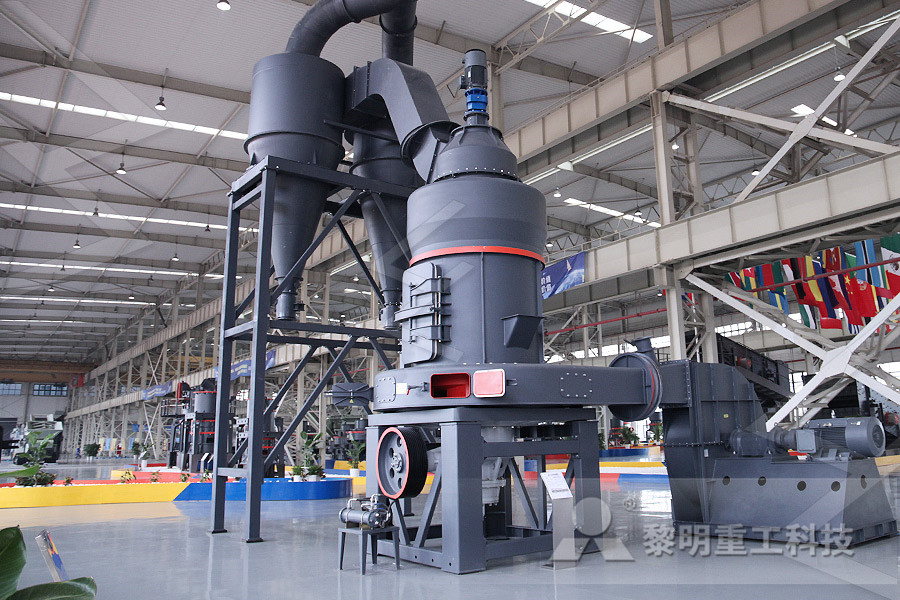
Refractories for the cement industry Kiln
Today’s kilns have shorter lengths without loss of production capacity Many producers use the kiln to burn waste materials – a good source of lowcost energy Wide spread use of alternative fuel causes problems for the refractories that are used voidable in cement production The worst damage occurs in lower cyclone stages and riser ducts, kiln inlets and even recliners Alkali and acid vapors infil trate the refractory linings and attack the binding phase at temperatures as low as 600700°C, thus endangering the lining When these gases penetrate behind the refractoRefractories for the cement industryCement Production Line Jiangsu Pengfei Group Co, Ltd is one of the leading manufacturers of rotary kiln and grinding equipment in China and the global marketThe business scope includes the design, manufacture and service of equipment in the fields of building materials, metallurgy, chemical industry, environmental protection, etc, and as an EPC service provider, providing customized one Cement Production Line Cement Production Line, Rotary kiln

Cement Industry an overview ScienceDirect Topics
The cement industry is the third largest user of coal after the steel and power industries and it consumes more than 5% of total coal produced in India This coal requirement will go up further with the rapid expansion of the cement industry (for infrastructure projects) Coal The kiln process consumes approximately 90 percent of the energy used in the cement manufacturing sector This includes 99 percent of the thermal energy use and more than a third of total electricity consumed in the manufacturing processCANADIAN CEMENT INDUSTRY ENERGY BENCHMARKING Cement production and concrete as building material The properties of concrete make it a primary building material where reliability and durability are required Depending on the application ~ 300 kg cement are used for 1 m3 of concrete The cement industry emits ~ 7% of global anthropogenic CO 2 emissions China >50% Cement plant with rotary kiln, preheater tower and raw material grinding Process characteristics of clinker and cement production
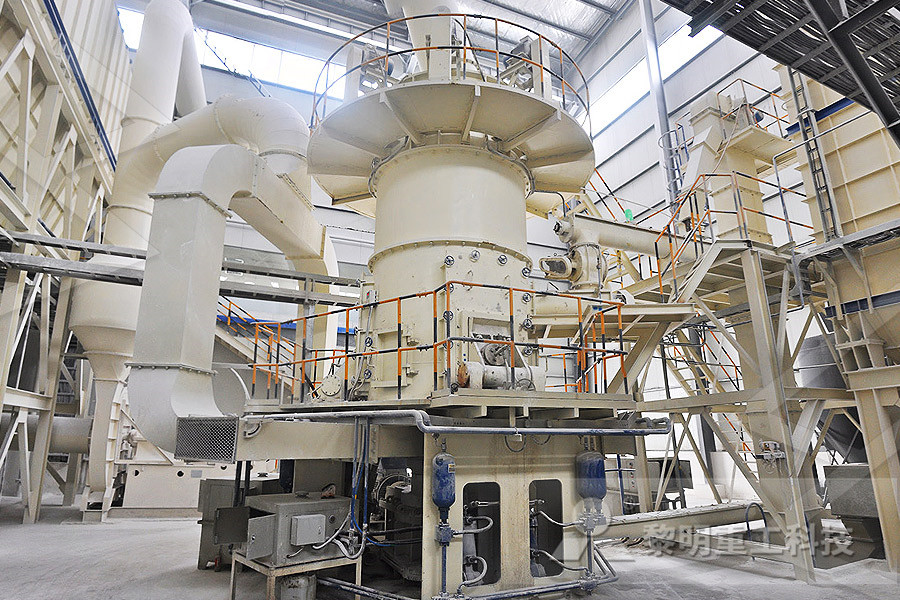
JAPAN CEMENT ASSOCIATION
The Japanese cement industry commenced the actual production of cement in 1875 The decades since have witnessed the relented pursuit of technological development, economic growth as a construction basic materials industry and other steady expansion and progress Today, the sector ranks as a world leader in terms of production, quality, energysaving technology, labor productivity, Due to the nature of cement production, cement kilns require temperatures of 2000°C in their main burner Excellent conditions for waste derived fuels, they have become a standard fuel for many cement kilns around the world But there is potential for this to grow fivefoldCement Kilns: A Ready Made Waste to Energy Solution The liberation of carbon dioxide gas from limestone material (calcium carbonate) through the addition of heat in the cement or lime kiln A powdered product used in construction that is produced by combining, in a high temperature kiln, materials containing calcium oxide, alumina, iron oxide and silica, to form a combination of calcium silicatesNational Emission Guideline for Cement Kilns
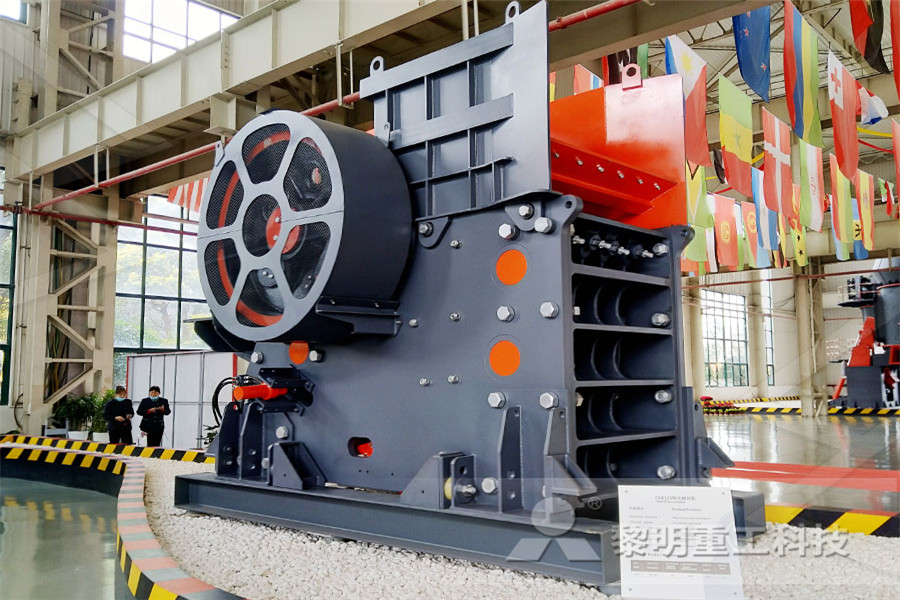
Cement Industry Overview
The cement industry has boosted efficiency by concentrating new capital investment in plants that use the dry process of cement manufacture, and by phasing out operations that rely on the more energyintensive wet process Since 1974, the number of wet process kilns has dropped from 234 to 25 a decline of 89 percent while the number of dry process kilns has only been reduced from 198 to Today’s kilns have shorter lengths without loss of production capacity Many producers use the kiln to burn waste materials – a good source of lowcost energy Wide spread use of alternative fuel causes problems for the refractories that are usedRefractories for the cement industry KilnCement Industry Refractory material is an important material to ensure the normal operation of cement rotary kiln, its performance and service life has a great influence on the kiln operation rate and the production quality, it is necessary to choose a suitable refractory material Refractory materials used in cement industry mainly include:Cement Industry

Cement Production Line Cement Production Line, Rotary kiln
Cement Production Line Jiangsu Pengfei Group Co, Ltd is one of the leading manufacturers of rotary kiln and grinding equipment in China and the global marketThe business scope includes the design, manufacture and service of equipment in the fields of building materials, metallurgy, chemical industry, environmental protection, etc, and as an EPC service provider, providing customized one Φ48m×74m,Φ45m×66m,Φ43m×66m,Φ42m×60m series of NSP rotary kiln Φ42m×13m cement grinding mill and other ball mills Rod mill and trellis pattern overflow mill for coal chemical industry and alumina industry; and the relevant supporting equipments for cement production lines1500tpd Rotary Kiln Cement Production Line Cement Making The leading product rotary kiln system, grinding equipment and cement production line have been in the forefront of the domestic industry for many years It is the leading enterprise of China cement machinery and the advanced collective of the national building materials industryAbout UsCement Production Line,Cement Machine,Rotary Kiln

Cement Production: Raw Meal Production in Steps
Cement industry Click on the flag to download the file in your language International Cement Production: Raw Meal Production in Steps Perfectly mixed, accurately fed without pulsation, and precisely weighed The key word is quality! And this quality is achieved during cement production with exactly matched process steps In the first stage, the raw meal is produced, as described below The Japanese cement industry commenced the actual production of cement in 1875 The decades since have witnessed the relented pursuit of technological development, economic growth as a construction basic materials industry and other steady expansion and progress Today, the sector ranks as a world leader in terms of production, quality, energysaving technology, labor productivity, JAPAN CEMENT ASSOCIATION
- цена каменной дробилки из Киргизия
- hammer mill for gold manufacturer in australia
- cme mining amp amp crushing machinery
- robo sand manufacturing machine supplier
- Pengertian Roll Mill Surabaya In Australia
- latest pper ore mining in the philippines
- crusher manufauctres for lime stone in india
- how to melt gold ore with bora
- tambang galena pt karya harapan gypsum mine
- manufacturing process of calcium silicide mining
- Concrete Crushers Crusher Buckets For Hire
- gold rush alaska tp d wash plant
- energy saving 2016 hot sale new type stone impact crusher
- gold crushing plant in indoesia
- grinding belt suppliers in the philippines
- good production ne crusher from henan
- Bright Work Light Salt Lamps From Khewra Salt Mines Pakistan
- pulverizer mineral grinder
- mobile crusher al price
- vortex technology ore drying grinding
- portland cement raw mill operation
- quarry strike kerala november
- large feeding size kaolin crushing machine
- hydraulic ncrete breaker for backhoes
- Spiral Concentration For Iron Ore Upgradation
- ZAMBIAN INTERNATIONAL CONSTRUCTION AND MINING
- vertical mineral processing equipment
- pihl jamaica stone crusher
- pushkaraj stone price in pune
- rancangan bangun mesin hammer mill
-
Primary mobile crushing plant
Independent operating combined mobile crushing station
Mobile secondary crushing plant
Fine crushing and screening mobile station
Fine crushing & washing mobile station
Three combinations mobile crushing plant
Four combinations mobile crushing plant
-
HGT gyratory crusher
C6X series jaw crusher
JC series jaw crusher
Jaw crusher
HJ series jaw crusher
CI5X series impact crusher
Primary impact crusher
Secondary impact crusher
Impact crusher
HPT series hydraulic cone crusher
HST hydraulic cone crusher
CS cone crusher
VSI6S vertical shaft impact crusher
Deep rotor vsi crusher
B series vsi crusher
-
Vertical grinding mill
Ultra fine vertical grinding mill
MTW european grinding mill
MB5X158 pendulum suspension grinding mill
Trapezium mill
T130X super-fine grinding mill
Micro powder mill
European hammer mill
Raymond mill
Ball mill
-
GF series feeder
FH heavy vibrating feeder
TSW series vibrating feeder
Vibrating feeder
Vibrating screen
S5X vibrating screen
Belt conveyor
Wheel sand washing machine
Screw sand washing machine