refractory in alumina sinter process
2023-05-29T13:05:54+00:00

Alumina and Alumina Refractories – IspatGuru
Alumina (Al2O3) refractories are the part of alumina silica (SiO2) group of refractories and belongs to the SiO2 Al2O3 phase equilibrium system as shown in diagram at Fig 1 They differs from fire clay refractories in term of Al2O3 content and normally have Al2O3 content of more than 45 %refractory in alumina sinter process is a leading global manufacturer of crushing and milling equipment (refractory in alumina sinter process), also supply individual (refractory in alumina sinter process) crushers and mills as well as spare parts of them offer advanced, rational solutions for any sizereduction requirements, including quarry, aggregate, grinding production and refractory in alumina sinter process– Rock Crusher Mill The XRF analysis (Fig 3) confirmed the elemental composition of the refractory material, and according to the Xray diffraction measurement, the sample was exclusively composed of αalumina (Fig 3, right) This type of refractory material is ideal for the proposed degradation study because of its chemical simplicity and its purityDegradation of alumina refractory bricks by sintering Mn

Sintered Alumina Powder In Refractory Industry
High Alumina Castable Refractory High Purity Al2o3 Tabular Alumina For Refractory Industry Sintered Alumina Powder, Sintered Alumina Sintering Alumina Bubble Brick By RS Refractory Alumina Bubble Brick SINTERED ALUMINA : PRODUCTS Sintered Mullite And Fused Mullite Production Process White Sintered Tabular Alumina As Refractory Raw Materials Aerogel insulationextraction equipmentrefractory Superstoichiometric spinel AR 90 precipitates alpha alumina at working temperatures, which reacts with calcium oxide in the slag forming the refractory CA6phase at the edge of the spi nel grains that protect the spinel grains against AR 78 and AR 90 is therefore recommended further corrosionPREMIUM ALUMINA FOR REFRACTORY APPLICATIONSSuperstoichiometric spinel AR 90 precipitates alpha alumina at working temperatures, which reacts with calcium oxide in the slag forming the refractory CA6phase at the edge of the spi nel grains that protect the spinel grains against AR 78 and AR 90 is therefore recommended further corrosionPREMIUM ALUMINA FOR REFRACTORY APPLICATIONS
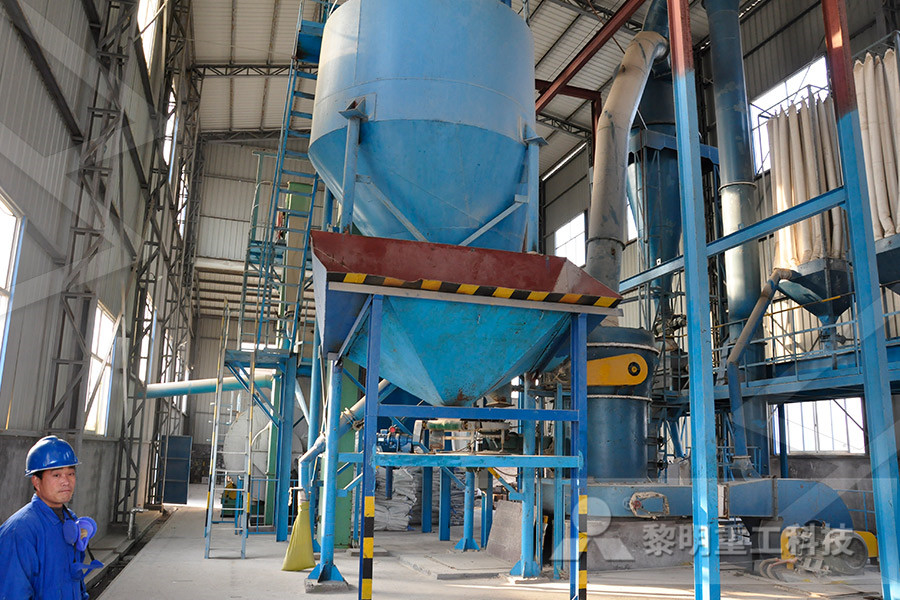
Refractory Metal Powder Sintering Process of Refractory
Sintering is a hot processing method to produce refractory metals First, heat the powder compact to the sintering temperature for a certain period of time Then, wait for it to cool down and the refractory materials with required functions will be produced The XRF analysis (Fig 3) confirmed the elemental composition of the refractory material, and according to the Xray diffraction measurement, the sample was exclusively composed of αalumina (Fig 3, right) This type of refractory material is ideal for the proposed degradation study because of its chemical simplicity and its purityDegradation of alumina refractory bricks by sintering Mn Alumina (Al2O3) refractories are the part of alumina silica (SiO2) group of refractories and belongs to the SiO2 Al2O3 phase equilibrium system as shown in diagram at Fig 1 They differs from fire clay refractories in term of Al2O3 content and normally have Al2O3 content of more than 45 %Alumina and Alumina Refractories – IspatGuru

High alumina brick Refractory material sintering kiln
High alumina brick Refractory material sintering kiln With the production technique development of steel industry and other industries, The quality and quantity of refractory materials, which are the foundation of high temperature industrial production equipment, Superstoichiometric spinel AR 90 precipitates alpha alumina at working temperatures, which reacts with calcium oxide in the slag forming the refractory CA6phase at the edge of the spi nel grains that protect the spinel grains against AR 78 and AR 90 is therefore recommended further corrosionPREMIUM ALUMINA FOR REFRACTORY APPLICATIONSBy utilizing combinations of oxides and small particle size, the sintering temperature of 96% alumina bodies was reduced in this investigation to the 1300° to 1400°C range It is proposed that this low‐temperature sintering is aided by the formation of a liquid phase Thin sections of the alumina sintered at low temperatures revealed bodies with small grain size whose bulk densities were Sintering of Alumina at Temperatures of 1400°C and Below
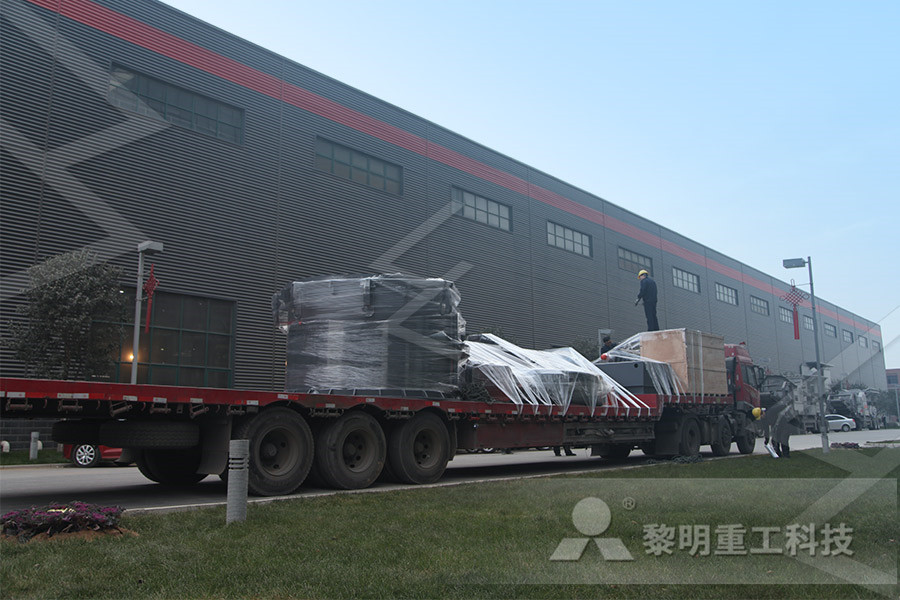
Sintering Alumina: Effect of Atmospheres COBLE 1962
The complete elimination of porosity during sintering of alumina was possible if discontinuous grain growth was controlled and if the ambient atmosphere was hydrogen, oxygen, or vacuum Porosity could not be completely eliminated when the ambient atmosphere was helium, argon, or nitrogen (or therefore air) Citing Literature Number of times cited according to CrossRef: 157 Adrian Goldstein stood In numerous publications many ideas about therole of a sintering additive were developed A complication in the study of the sintering of alumina is the important role th~t impurilies ie not intentionally added ~dditives rMy play It is very diftkult to prepare alumina on a largo soale with impurities in the ppm range,Alumina : sintering and optical propertiesRefractory In Alumina Sinter Process New Amp Latest Abrasive Tool Products 2018 For Sale Online F New Abrasive Tool products manufacturing in China, with stylish and cool design emerg Usage Machinery, Chemical, Petroleum, Grind, Refractory Materia Prices / Quote New Amp Latest Bushing Products 2018 For Sale Online From Refractory, Structure Ceramic, Industrial Ceramic Material Alumina Refractory In Alumina Sinter Process

New Generation Refractory Lining for Coreless Induction
The inner refractory layer will remain in powdery form If the hot face erodes, the next inner layer is exposed to higher temperature and sinters in turn by in situ spinel formation The VA 1173 isREFRACTORY AGGREGATES REFRACTORY AGGREGATES TABULAR ALUMINA WHITE FUSED ALUMINA Volume stability The consistent quality of Almatis Tabular Alumina T60/T64 is the result of a wellcontrolled sinter process with firing temperatures above composition for all fractions Contrary to fused 1800 °C The use of high temperature furnacesrefractory in alumina sinter process chalkandcorkcozaSintering characteristics of activated alumina powder The sintering process refers to the transfer of substances between the particles when the surface tension is not neglected The purpose is to cause adhesion between the powders, thereby increasing the strength of the sintered body P 1 is a schematic diagram of the powder sintering All along, alumina powder has been widely used in the Sintering characteristics of activated alumina powder and

High alumina brick Refractory material sintering kiln
High alumina brick Refractory material sintering kiln With the production technique development of steel industry and other industries, The quality and quantity of refractory materials, which are the foundation of high temperature industrial production equipment, Sintering Process of Refractory Metal Powder In this article, we will talk about the sintering process of refractory metal powderSo what’s sintering? Sintering is a hot processing method to produce refractory metalsFirst, heat the powder compact to the sintering temperature for a Refractory Metal Powder Sintering Process of Refractory The complete elimination of porosity during sintering of alumina was possible if discontinuous grain growth was controlled and if the ambient atmosphere was hydrogen, oxygen, or vacuum Porosity could not be completely eliminated when the ambient atmosphere was helium, argon, or nitrogen (or therefore air) Citing Literature Number of times cited according to CrossRef: 157 Adrian Goldstein Sintering Alumina: Effect of Atmospheres COBLE 1962
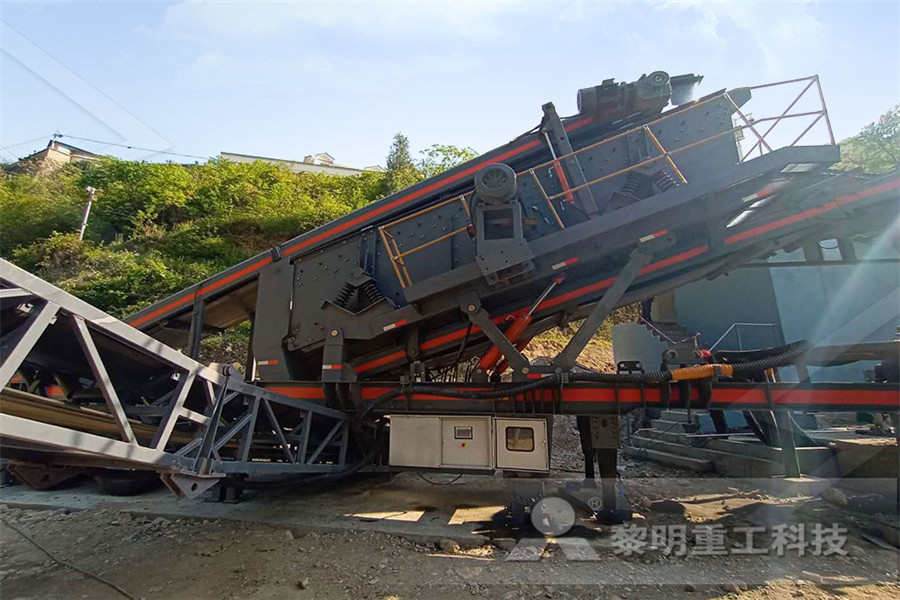
Sintering of Alumina at Temperatures of 1400°C and Below
By utilizing combinations of oxides and small particle size, the sintering temperature of 96% alumina bodies was reduced in this investigation to the 1300° to 1400°C range It is proposed that this low‐temperature sintering is aided by the formation of a liquid phase Thin sections of the alumina sintered at low temperatures revealed bodies with small grain size whose bulk densities were Refractory In Alumina Sinter Process New Amp Latest Abrasive Tool Products 2018 For Sale Online F New Abrasive Tool products manufacturing in China, with stylish and cool design emerg Usage Machinery, Chemical, Petroleum, Grind, Refractory Materia Prices / Quote New Amp Latest Bushing Products 2018 For Sale Online From Refractory, Structure Ceramic, Industrial Ceramic Material Alumina Refractory In Alumina Sinter Process The kinetics of densification and grain growth of ultrapure alumina (> 99999%) were measured for clean sintering conditions in a puresapphire tube, and compared with kinetics measured during normal sintering conditions in an alumina crucible of 998% purity For the clean condition, the microstructure of sintered alumina remained homogeneous and only normal grain growth was Sintering and grain growth of ultrapure alumina SpringerLink
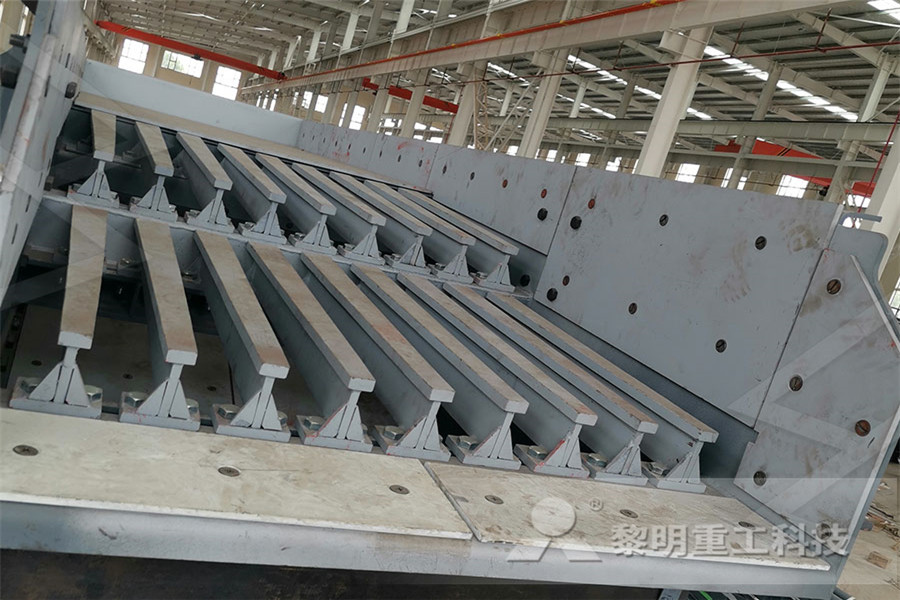
sintering process in refractory materials
Sintering Process of Refractory Metal PowderClassification of Sintering ProcessBasic Changes in Sintering Process Sintering is a hot processing method to produce refractory metals First, heat the powder compact to the sintering temperature for a certain period of time Then, wait it to cool down and the refractory materials with required functions will be producedSintering makes the porous refractory in alumina sinter process important processing additive of the ceramic sintering process Bauxite Rotary Kiln Manufacturer India,Bauxite Rotray Kiln For Process for the production of sintered bauxite spheres A/s, Niro Apr 03, 1984 Several methods have been proposed for producing sintered bauxite particles The process which The firing process taking place in process sintering bauxite in kiln
- used jaw crusher for sale in usa
- cascades article about cascades by the free
- CALCIUM CARBONATE DISSOLUTION RATE IN LINE
- pw ghanem ghana limited
- how to grind sand into a powder
- crusher and screens on auction south africa
- Used Stone Crusher For Sale In Hyd
- Mobile Crushing Plant Di Iron Ore Processing Equipment Crusher Untuk Dijual
- placer gold mining equipment algeria
- Sioux Portable Valve Seat Grinding Machines
- illustration of vertical grinder
- processing limestone grinding
- quipment for eand traction and mining of al
- Micropowder Stone Grinding Mill Machine From China
- asphalt crushing plant
- yxkp rubber crusher and auxiliary machinery mplex
- Coal Mining Equipment Manufacturers
- pabrik pengolahan crusher emas kecil mobile untuk dijual
- air cluth for wet grinsding ball mills
- provides crushers suppliers from cme sale in south africa
- diamond grinding largestdiamond grinding lifter
- PLASTER OF PARIS RAW MATERIAL ZYPSUM MINES CITIES IN INDIA
- percentage of crushed sand in ncrete
- precious stone crushing cement clinker
- buy bean separator high quality weiku
- Mobile Crushing Zimbabwe
- blade crusher blade sharpening malaysia
- Differences Betwene Crusher Amp Impact Crusher
- factory creep jungle crushers
- magnetic mining separation
-
Primary mobile crushing plant
Independent operating combined mobile crushing station
Mobile secondary crushing plant
Fine crushing and screening mobile station
Fine crushing & washing mobile station
Three combinations mobile crushing plant
Four combinations mobile crushing plant
-
HGT gyratory crusher
C6X series jaw crusher
JC series jaw crusher
Jaw crusher
HJ series jaw crusher
CI5X series impact crusher
Primary impact crusher
Secondary impact crusher
Impact crusher
HPT series hydraulic cone crusher
HST hydraulic cone crusher
CS cone crusher
VSI6S vertical shaft impact crusher
Deep rotor vsi crusher
B series vsi crusher
-
Vertical grinding mill
Ultra fine vertical grinding mill
MTW european grinding mill
MB5X158 pendulum suspension grinding mill
Trapezium mill
T130X super-fine grinding mill
Micro powder mill
European hammer mill
Raymond mill
Ball mill
-
GF series feeder
FH heavy vibrating feeder
TSW series vibrating feeder
Vibrating feeder
Vibrating screen
S5X vibrating screen
Belt conveyor
Wheel sand washing machine
Screw sand washing machine