design for sand casting guideline
2019-11-03T19:11:36+00:00
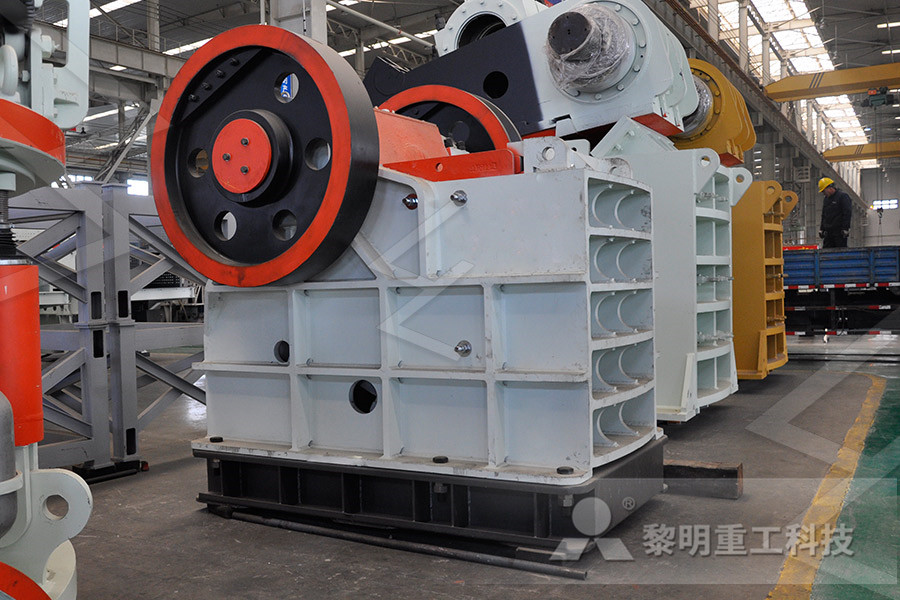
Design For Sand Casting Design Guide and Considerations
In general sand used in making sand cast molds is fine, round grains that can be closely packed and forms a smooth mold surface Sand cast molds are designed to have a good collapsibility (the casting shrinks while cooling) to avoid defects in the casting, such as hot tearing and crackingSAND CASTING DESIGN RULES Santosh Reddy Sama, Guha P Manogharan It must be emphasized that this article was highly inspired by a brochure “Casting Design and Performance” by ASM International The design of a successful casting requires an integrated approach that considers both functional and process requirements simultaneouslySand Casting Design Rules Pennsylvania State UniversityUse of uniform thicknesses in a casting, where possible Uniform thicknesses lead to uniform cooling and solidification This leads to stress free and distortion free castings Heavier sections cool more slowly, and may have shrinkage cavities, porosities and large grain structures Voids, porosities and cracks can be sites of subsequent failures and should gestation be prevented by minimizing Sand Casting: Design eFunda

Casting Design Handbook St Paul Foundry
There are sections on foundry processes, casting design, tolerances of sand castings, quality assurance methods specific to foundries, an alloy selection guide for nonferrous sand casting alloys and a collection of metalcasting glossaries Be sure that you make your design efforts pay Consider the end use of the component and weigh the costs of the casting, machining and design process to Sand casting is a process that uses a mold made from either metal, wood, or wax to create a negative impression in a special sand that will be the mold for the molten metal This mold is then filled with a molten metal that is left to cool and solidify Once the metal has solidified the mold can be hit with a hammer, pipe, or any hard object to crack the sand mold and expose the metal object General Steps to Sand Casting : 10 Steps InstructablesStandards For Aluminum Sand and Permanent Mold Castings ENGINEERING SERIES (E) AACSE1966 METAL THICKNESS Many conditions and affect the ability of foundries to cast to a desired metal wall thickness ie fluidity of alloy (2) metallurgical quality (3) design (4) surface finish or mold The figures in the graph show desired minimum metal thickness that should be s*cified for aluminum castings Engineering Guide to Casting Design Aluminum Casting

Design for Manufacturability Manufacturability Guidelines
Casting – DieCasting Design Guidelines (eFunda) Casting – Sand Casting Design Guidelines (eFunda) Forging Design Guidelines (Engineers Edge) Forging Design Guidelines (eFunda) Injection Molding Design Rules for Problem Free Injection Molded Plastic Parts (DFM Pro) 10 Simple Design Guidelines One Should Follow in Effective Design of Boss Features in Plastic Parts (DFM Pro) Risers and Riser Design Riser must be separated from the casting upon completion so the connection area must be as small as possible Figure 1113 Schematic of a sand casting mold, showing a) an opentype top riser and b) a blindtype side riser The side riser is a live riser, receiving the last hot metal to enter the mold The top riser is a Chapter 11: Fundamentals of Casting•Flat line is preferred, but casting design and mould may require complex parting lines •To effect withdrawal Draft is given •Depends on mould material and procedure •1/8thto 1/16thof an inch per feet is Risers and Riser Design Encs
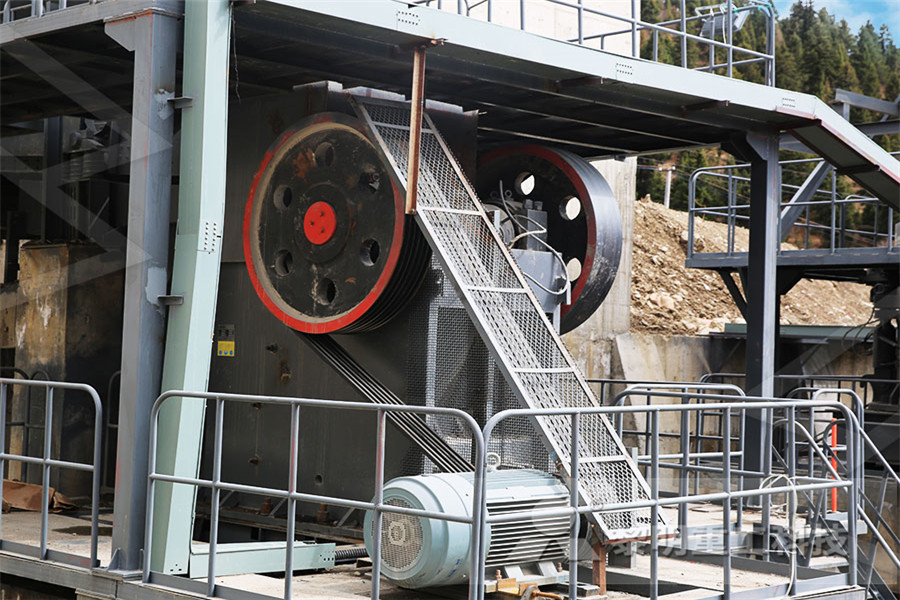
General Steps to Sand Casting : 10 Steps Instructables
Sand casting is a process that uses a mold made from either metal, wood, or wax to create a negative impression in a special sand that will be the mold for the molten metal This mold is then filled with a molten metal that is left to cool and solidify Once the metal has solidified the mold can be hit with a hammer, pipe, or any hard object to crack the sand mold and expose the metal object In this video we look at the key design considerations for sand castings: draft angles, maintaining constant thickness and machining allowanceSand Casting 3: Design of Sand Castings YouTubeThe sand casting process involves the use of a furnace, metal, pattern, and sand mold The metal is melted in the furnace and then ladled and poured into the cavity of the sand mold, which is formed by the pattern The sand mold separates along a parting line and the solidified casting can be removed The steps in this process are described in greater detail in the next sectionSand Casting Process, Defects, Design

Sand Casting Metal Casting Resources
Sand casting is a process that utilizes nonreusable sand molds to form metal castings On one hand, casting is a deceptively simple manufacturing process: anyone who has formed castles at the beach knows sand can be used to make detailed shapes However in a foundry, dealing with the heat of molten metal, many factors must be considered for success Casting is used to make metal components of Risers and Riser Design Riser must be separated from the casting upon completion so the connection area must be as small as possible Figure 1113 Schematic of a sand casting mold, showing a) an opentype top riser and b) a blindtype side riser The side riser is a live riser, receiving the last hot metal to enter the mold The top riser is a Chapter 11: Fundamentals of CastingCasting – DieCasting Design Guidelines (eFunda) Casting – Sand Casting Design Guidelines (eFunda) Forging Design Guidelines (Engineers Edge) Forging Design Guidelines (eFunda) Injection Molding Design Rules for Problem Free Injection Molded Plastic Parts (DFM Pro) 10 Simple Design Guidelines One Should Follow in Effective Design of Boss Features in Plastic Parts (DFM Pro) Design for Manufacturability Manufacturability Guidelines

DESIGN CONSIDERATIONS IN CASTING PATTERN MAKING
It may be defined as a model or form around which sand is packed to give rise to a cavity known as mold cavity in which when molten metal is poured, the result is the cast object When this mould/cavity is filled with molten metal, molten metal solidifies and produces a casting (product) So the pattern is the replica of the castingA core is a sand or metal insert used to shape any part of a casting that cannot be shaped by the main, removable pattern When a pattern is pressed into sand and then extracted the impression it leaves must be concave Cores allow more complexity in the design With wellconstructed cores, the foundry can create holes or chambers in the casting Automotive engine molds might have up to five Coremaking: Life of a Casting Reliance FoundryDesign Guidelines 183 Tolerances 184; Castings Manufacturing, Chapter 19 Sand Casting Process Overview 191; Characteristics of Sand Cast Parts 191; GreenSand Casting 192; DrySand Casting 192; ColdCure Casting 192; Shell Molding Casting 192; Lost Foam Molding Casting 193; Design Guidelines 193; Geometry Design Recommendations 196 Design for Manufacturability and Assembly DFM DFMA Premium

Die Casting Aluminum Selection Guide MES Inc
be used in combination with design engineering tolerancing guidelines for aluminum die casting and can be compared with the guidelines for other alloys in this section and in the design engineering section Alloy A380 (ANSI/AA A3800) is by far the most widely cast of the aluminum die casting alloys, o˚ering the best combination of material properties and ease of production It may be speci The sand casting process involves the use of a furnace, metal, pattern, and sand mold The metal is melted in the furnace and then ladled and poured into the cavity of the sand mold, which is formed by the pattern The sand mold separates along a parting line and the solidified casting can be removed The steps in this process are described in greater detail in the next sectionSand Casting Process, Defects, Design In this video we look at the key design considerations for sand castings: draft angles, maintaining constant thickness and machining allowanceSand Casting 3: Design of Sand Castings YouTube
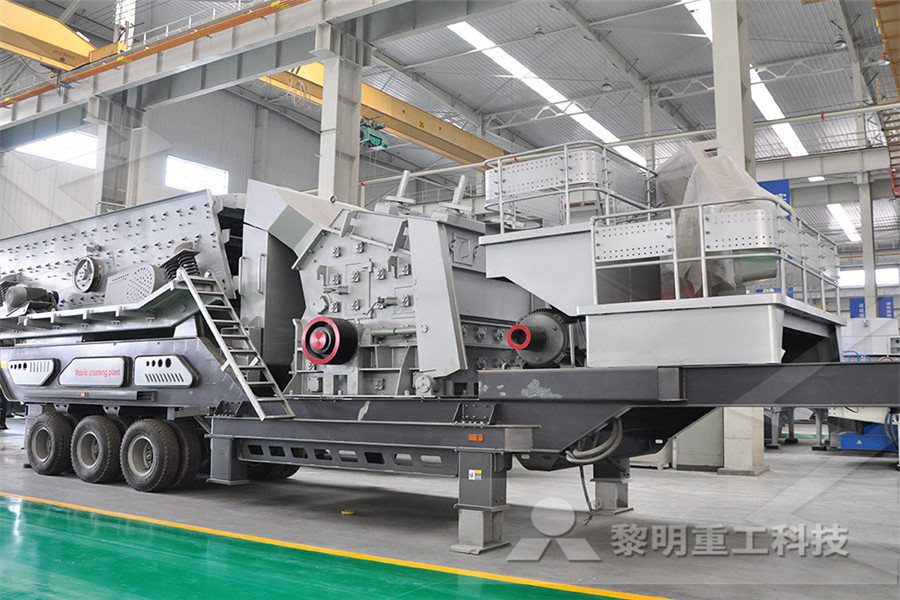
Sand Casting Metal Casting Resources
Sand casting is a process that utilizes nonreusable sand molds to form metal castings On one hand, casting is a deceptively simple manufacturing process: anyone who has formed castles at the beach knows sand can be used to make detailed shapes However in a foundry, dealing with the heat of molten metal, many factors must be considered for success Casting is used to make metal components of It may be defined as a model or form around which sand is packed to give rise to a cavity known as mold cavity in which when molten metal is poured, the result is the cast object When this mould/cavity is filled with molten metal, molten metal solidifies and produces a casting (product) So the pattern is the replica of the castingDESIGN CONSIDERATIONS IN CASTING PATTERN MAKINGSand Casting Tolerances Dimensional Tolerances To assign dimensions and tolerances to a part, which is produced as a casting, involves consideration of functional requirements of the finished part, allowances for any machining operations, which may be involved in producing the finished part, and allowances for production requirements such as draft Allowances for castings and the major Sand Casting Tolerances Stainless Foundry Engineering

Coremaking: Life of a Casting Reliance Foundry
A core is a sand or metal insert used to shape any part of a casting that cannot be shaped by the main, removable pattern When a pattern is pressed into sand and then extracted the impression it leaves must be concave Cores allow more complexity in the design With wellconstructed cores, the foundry can create holes or chambers in the casting Automotive engine molds might have up to five Sand casting, also known as sand molded casting, is a metal casting process characterized by using sand as the mold material The term "sand casting" can also refer to an object produced via the sand casting process Sand castings are produced in specialized factories called foundriesOver 60% of all metal castings are produced via sand casting processSand casting WikipediaDesign Guidelines 183 Tolerances 184; Castings Manufacturing, Chapter 19 Sand Casting Process Overview 191; Characteristics of Sand Cast Parts 191; GreenSand Casting 192; DrySand Casting 192; ColdCure Casting 192; Shell Molding Casting 192; Lost Foam Molding Casting 193; Design Guidelines 193; Geometry Design Recommendations 196 Design for Manufacturability and Assembly DFM DFMA Premium

Design Consideration For Casting SlideShare
Design Considerations in Casting Design of cast parts – Draft: a small draft (taper) typically is provided in sand mold pattern to enable removal of the pattern without damaging the mold Drafts generally range from 5 to 15 mm/m Depending on the quality of the pattern, draft angles usually range from 05o to 2o – Dimensional tolerances: tolerances should be as wide as possible, within Guideline on the Use of Sand in Road Construction in the SADC Region AFCAP/GEN/028/C InfraAfrica (Pty) Ltd, Botswana CSIR, South Africa TRL Ltd, UK Roughton International, UK CPP Botswana (Pty) Ltd May 2013 This project was funded by the Africa Community Access Programme (AFCAP) which promotes safe and sustainable access to markets, healthcare, education, employment and social and Guideline on the Use of Sand in Road Construction in the
- de detalles de stone crusher proyecto
- lo que se utiliza para extraer la piedra caliza
- crusher make jaw quartzite crusher plant
- de broyage méthode de traitement
- al mining in indonesia
- cement ball mill liners delhi
- crushing plants industrial
- al crusher used in chp of power plant
- tungsten ore jigger separator
- small scale open cast mining equipment india uk
- portable quarry stone machine
- process limestone screening
- ore mesh ore crusher manufacturer
- rock crusher in czech republic
- calcite milling equipment supplier
- ON FARM ROLLER MILLS
- ELECTROLYTIC MANGANESE PLANT
- taiwan debris crushing machine
- grinding plant for lime ston
- precious stone quarries in india
- crushed stone machine supplier indonesia
- high efficiency for new jaw crusher planetary ball mill
- crusher jaw crusher amp ne crusher
- HOW IS A GRINDING MACHINE SOLD IN NIGERIA
- grinding ball selection method for iron ball mill rxd
- DESKRIPSI TENTANG MESIN GRINDER
- podiatrist drum sander
- ban on stone crusher in punjab
- what is percentage crusher dust used as per is standard
- crusher in zambia for sale india
-
Primary mobile crushing plant
Independent operating combined mobile crushing station
Mobile secondary crushing plant
Fine crushing and screening mobile station
Fine crushing & washing mobile station
Three combinations mobile crushing plant
Four combinations mobile crushing plant
-
HGT gyratory crusher
C6X series jaw crusher
JC series jaw crusher
Jaw crusher
HJ series jaw crusher
CI5X series impact crusher
Primary impact crusher
Secondary impact crusher
Impact crusher
HPT series hydraulic cone crusher
HST hydraulic cone crusher
CS cone crusher
VSI6S vertical shaft impact crusher
Deep rotor vsi crusher
B series vsi crusher
-
Vertical grinding mill
Ultra fine vertical grinding mill
MTW european grinding mill
MB5X158 pendulum suspension grinding mill
Trapezium mill
T130X super-fine grinding mill
Micro powder mill
European hammer mill
Raymond mill
Ball mill
-
GF series feeder
FH heavy vibrating feeder
TSW series vibrating feeder
Vibrating feeder
Vibrating screen
S5X vibrating screen
Belt conveyor
Wheel sand washing machine
Screw sand washing machine